What’s Inside a RetroFoam Injection Foam Insulation Trailer?
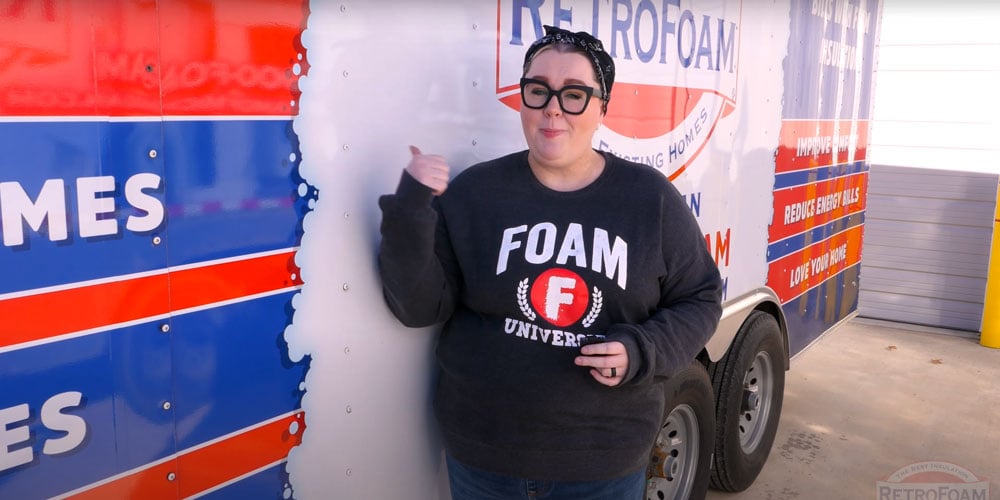
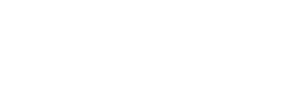
When you think about foam insulation, your first thought probably isn’t about the equipment used to install it.
But let me tell you – what’s inside a foam insulation trailer makes all the difference in delivering a premium product like RetroFoam.
If you’ve ever wondered about the magic that happens behind the scenes, this article will take you inside the injection foam rig. It will break down its components, their functions, and why they’re crucial to the quality of the insulation in your walls.
Why Does What's Inside the Foam Insulation Trailer Matter?
Homeowners rarely think about the process behind installing foam insulation.
Most just want the job done quickly and without issues. But, the science and technology inside the rig ensure that RetroFoam lives up to its reputation as a premium insulation product.
The Key Components of a RetroFoam Insulation Trailer
Let’s break it down, piece by piece, so you can understand why this matters for your home.
1. The Mixing Tanks
At the heart of the trailer are two tanks: one for the resin and another for the foaming agent.
These tanks combine the dry resin product and the foaming agent with water. But it’s not just about mixing – it’s about precision.
- Dry Resin Mixing: The crew pours the dry resin into a basin, which is then funneled into a water tank.
- Foaming Agent Mixing: The foaming agent is poured into a separate tank containing water.
Both tanks are heated to 120 degrees Fahrenheit, a critical temperature that ensures the resin and foaming agent mix properly. A water heater is installed in the trailer to maintain this consistent temperature, ensuring optimal conditions every time.
2. The Circulation Process
The mixing process isn’t a simple dump-and-stir operation.
- Water is pumped into the tanks and circulated continuously for about 20 minutes. This creates a homogenous mixture and ensures everything is ready for application.
- The hoses – color-coded red, blue, and yellow – transport resin, air, and foaming agent throughout the system.
This careful mixing ensures that the foam is the perfect consistency when it’s ready to be injected into your walls.
3. The Pump System
Once the resin and foaming agent are mixed, they’re pulled through hoses into a central pump.
This pump combines the two components just before they are injected into the wall cavities.
This process's precision guarantees that the foam fills every nook and cranny in your walls, providing superior insulation and sound dampening.
4. The Power Trio: Generator, Compressor, and Water Heater
To keep everything running smoothly, the trailer houses three essential pieces of equipment:
- Generator: Powers the entire rig, from the pump to the mixing tanks.
- Air Compressor: Provides the pressure needed to inject foam into wall cavities effectively.
- Water Heater: Maintains the critical 120-degree temperature for the water in the mixing tanks.
These components ensure that the crew can work efficiently while maintaining the high standards for which RetroFoam is known.
Quality Control: Testing the Product
Before any foam is injected into your walls, the crew performs rigorous testing to ensure it meets RetroFoam’s quality standards.
- Air Pressure Testing: Ensures the foam is injected at the right consistency and pressure.
- Foam Quality Checks: If the mixture isn’t perfect, the crew starts the process over from scratch.
This commitment to quality ensures that you always receive the premium product you expect from RetroFoam.
Why This Matters for Your Home
Understanding what’s inside the trailer helps you see why RetroFoam is a cut above other insulation products.
Every piece of equipment in the trailer is there for a reason – working together to deliver foam insulation that’s energy-efficient, durable, and tailored to your home’s needs.
Ready to Upgrade Your Insulation?
Now that you’ve seen the inner workings of a foam insulation trailer, you might be ready to take the next step.
Head over to the Dealer Finder on our website to connect with a local RetroFoam dealer.
Remember, this isn’t just insulation – it’s science. And when it comes to your home, science makes all the difference.
Related Articles
Can Injection Foam Insulation Be Installed as a DIY Project?
What to Look for When Hiring an Insulation Contractor
Hiring an Insulation Contractor? Why the Cheapest Quote Could Cost You More
About Amanda Emery
Amanda previously has worked as a breaking news and crime reporter, TV news producer, and editor. As a journalist, she has won several awards from The Society of Professional Journalists - Detroit Chapter and the Michigan Press Association. Amanda uses her experience as a journalist to write content that will help educate homeowners on foam insulation benefits. When Amanda isn’t writing, she’s spending time with her husband Chris, daughter Lilith-Maeve, and rescued huskies Danger and Wendigo. She also loves knitting, making art, and cooking.